Y-strainers are the unsung heroes of a piping system, quietly ensuring the smooth operation of thermoplastic piping systems. In this blog post, we embark on a journey to explore the form and function of inline Y-strainers, shedding light on their importance and versatility in modern fluid management.
Understanding the Form:
Inline Y-strainers derive their name from their distinctive Y-shaped design. Crafted from robust thermoplastics like PVC (polyvinyl chloride), CPVC (chlorinated polyvinyl chloride), or PP (polypropylene), these strainers boast exceptional durability and corrosion resistance. Their form comprises a cylindrical body with an inlet and outlet port positioned at the top and bottom of the Y, respectively. Within the body resides a perforated screen or mesh, meticulously engineered to capture unwanted particles while allowing fluid to flow freely.
Functionality Unveiled:
At its core, the function of an inline Y-strainer is to safeguard downstream equipment and processes by filtering out debris, sediment, and other contaminants from the fluid stream. The operation is elegantly simple yet immensely effective:
1. Filtration: As fluid flows through the piping system, the Y-strainer intercepts any solid particles suspended in the fluid. These particles, ranging from rust flakes to debris, are trapped by the perforated screen, preventing them from reaching sensitive components such as pumps, valves, and instruments downstream.
2. Maintenance of System Integrity: By preventing debris from entering downstream equipment, inline Y-strainers mitigate the risk of damage and premature wear, thus prolonging the lifespan and reliability of the entire fluid handling system. This proactive approach to maintenance helps minimize downtime and operational costs.
3. Pressure Drop Management: While the primary function of inline Y-strainers is filtration, they also play a role in managing pressure drops within the piping system. The perforated screen design ensures minimal disruption to fluid flow, maintaining optimal pressure levels while effectively capturing contaminants.
Applications Across Industries:
1. Chemical Processing: In chemical processing plants, where the integrity of fluid streams is paramount, inline Y-strainers are employed to protect sensitive equipment such as pumps, meters, and control valves from damage caused by particulate matter.
2. Water Treatment: Municipal water treatment facilities rely on inline Y-strainers to filter out sediment, algae, and other impurities from raw water sources, ensuring the purity and safety of the treated water supply.
3. Food & Beverage: From foodstuffs to pharmaceutical manufacturing, inline Y-strainers find application in a myriad of industrial processes where maintaining clean fluid streams is essential for product quality and regulatory compliance.
4. Process Cooling: Heating, ventilation, and air conditioning (HVAC) systems utilize inline Y-strainers to remove debris and contaminants from cooling water loops, safeguarding heat exchangers and chillers from fouling and corrosion.
Conclusion:
Inline Y-strainers offer effective filtration capabilities within compact and reliable designs. As industries continue to evolve and demand greater efficiency and reliability from their fluid handling systems, the role of inline Y-strainers will only grow in significance. By embracing these indispensable components, engineers and operators can ensure the longevity, efficiency, and integrity of their thermoplastic piping systems, driving progress and innovation in fluid management practices.
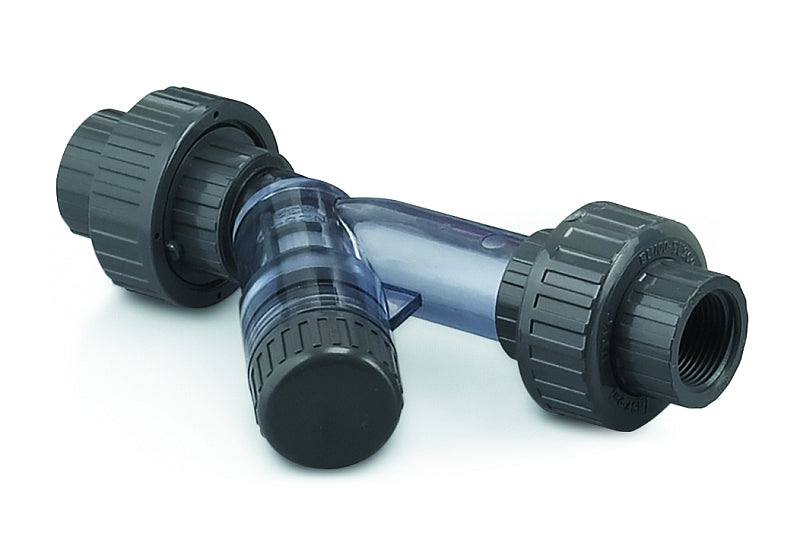